Key Information and Steps for Customizing Roll Cage
Customizing roll cage is an important process that involves improving the safety performance of automobiles. Here are some key information and steps about customizing roll cage:
1、 Clear design requirements
Before customizing a roll cage, it is necessary to first clarify the design requirements. This includes determining the size, shape, material, and expected collision energy absorption capacity of the roll cage. The design requirements should be based on the size, purpose, and safety performance requirements of the vehicle.
2、 Material selection
The material selection of the anti roll frame is crucial, as it directly affects the strength, weight, and corrosion resistance of the anti roll frame. Common materials include:
High strength steel: It has good strength and toughness, and can withstand large collision impact forces.
Aluminum alloy: Lightweight and strong, with good corrosion resistance, it is one of the preferred materials for customized roll cage.
Carbon fiber: Despite its high cost, it has extremely high strength and low weight, making it suitable for vehicles with strict weight requirements.
3、 Structural Design
The structural design of the roll cage should be able to absorb collision energy to the maximum extent possible and disperse it to other parts of the vehicle, thereby protecting the safety of passengers.
4、 Manufacturing process
The manufacturing process of customized roll cage usually includes steps such as material cutting, bending forming, welding, and surface treatment. These steps require high-precision equipment and professional technicians to ensure the quality and performance of the roll cage.
Material cutting: Using laser cutting or mechanical cutting methods to cut materials into the desired shape and size.
Bending Forming: Using professional bending equipment, the cut material is bent into the desired shape.
Welding: Using high-quality welding equipment and processes, various components are welded together to form a complete roll cage structure.
Surface treatment: Surface treatment of the welded anti roll frame, such as sandblasting, painting, etc., to improve its corrosion resistance and aesthetics.
5、 Testing and Adjustment
The customized roll cage needs to undergo rigorous testing and adjustment to ensure that it meets the expected safety performance requirements. Testing usually includes collision testing, vibration testing, and durability testing. According to the test results, necessary adjustments and optimizations can be made to the roll cage to improve its performance.
6、 Installation and Debugging
Finally, install the customized roll cage onto the vehicle and debug it. During the debugging process, it is necessary to ensure that the roll cage fits tightly with other parts of the vehicle and does not have a negative impact on the vehicle's driving performance.
Qingdao Feiyuan Storage Equipment Co., ltd. is a manufacturer of storage and logistics facilities that integrates research and development, production, and sales. For more information about custom roll cage, please contact us.
Address:Lime KiIn Industrial Zone, Wangtai Town, Huangdao District,Qingdao, China.
Email:admin@fyracks.com
Hot keywords:
custom roll cage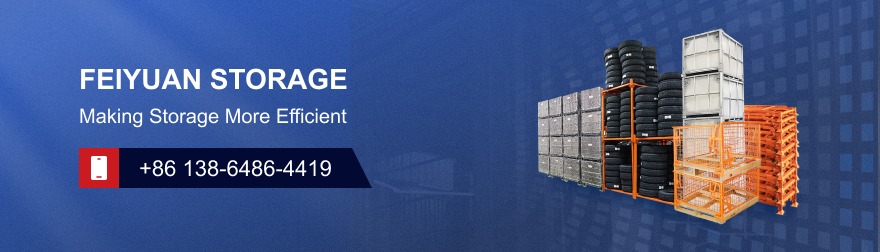
What are the Characteristics of Floor Tire Storage Racks?
The floor tire storage rack is the core equipment in the tire storage, turnover and production links. Its design must take into account storage efficiency, safety and space utilization. The following systematically analyzes its core features from four dimensions:


Key Points for Selecting Car Tire Storage Racks
The selection of car tire storage racks needs to be combined with tire characteristics, storage environment and management requirements, focusing on the five core elements of load-bearing capacity, space adaptability, access efficiency, safety protection and cost-effectiveness.


What are the Application Scenarios of Stackable Stillages?
Stackable stillages are widely used in a variety of industries and scenarios due to their flexibility and space utilization advantages. The following is a classification description by industry and specific needs


What are the Characteristics of Tire Rack Shelving?
Tire racks shelving are equipment for storing tires, which are widely used in automobile maintenance, parts management, logistics packaging and other fields. The following is an introduction to the characteristics of tire racks shelving

